- Medical devices class I
- 30 Nov. 2023
Approval of class I medical devices
- What are medical devices?
- What does class I mean?
- Which medical devices are in class I (examples)?
- What are the deadlines?
- What does it mean to be a manufacturer?
- Outsourcing of production and procurement of raw materials
- How to fulfil the MDR?
- Quality management system
- Technical documentation
- Preparation of an EU declaration of conformity
- Logging in to DMIDS
- Maintenance of the technical documentation
- Local Inspectorate & Inspections - Help! What now?
- Classification dispute: My product is Class I - the local authority sees it differently.
What are medical devices?
Simply put, medical devices are products that fulfil a medical purpose and have a significant physical effect in order to develop their performance. In order to really determine precisely whether or not a medical device is involved in the case at hand, it is necessary to check against the definition:
"Medical device" means an instrument, apparatus, appliance, software, implant, reagent, material or other article which, according to the manufacturer, is intended for human use and is intended to fulfil, alone or in combination, one or more of the following specific medical purposes:
- Diagnosis, prevention, monitoring, prediction, prognosis, treatment or alleviation of disease,
- Diagnosis, monitoring, treatment, alleviation of or compensation for injuries or disabilities,
- Examination, replacement or alteration of the anatomy or of a physiological or pathological process or condition,
- Obtaining information through the in vitro examination of samples derived from the human body - including from organ, blood and tissue donations.
...and whose principal intended action in or on the human body is not achieved by pharmacological or immunological means or metabolically, but whose mode of action may be supported by such means.
The following products are also considered medical devices:
- Products for contraception or promotion of conception.
- products specifically intended for the cleaning, disinfection or sterilisation of the products referred to in Article 1(4) and the products referred to in paragraph 1 of this indent.
What does class I mean?
Medical devices are classified into classes I, IIa, IIb, and III. The lowest class (1 or I) is for devices with a low risk for patients. The higher the risk class, the higher the underlying risk of the respective medical device.
Admittedly, some medical devices are classified under the MDR in risk classes that may seem somewhat exaggerated. However, this cannot be changed - strictly all classification rules of the MDR must be taken into account. The highest risk class resulting from the application of all classification rules therefore determines the actual risk class of a product.
Which medical devices are in class I (examples)?
- Wheelchairs and many other aids
- Plasters and compresses
- Physiotherapy couches
- Reusable surgical instruments
- etc.
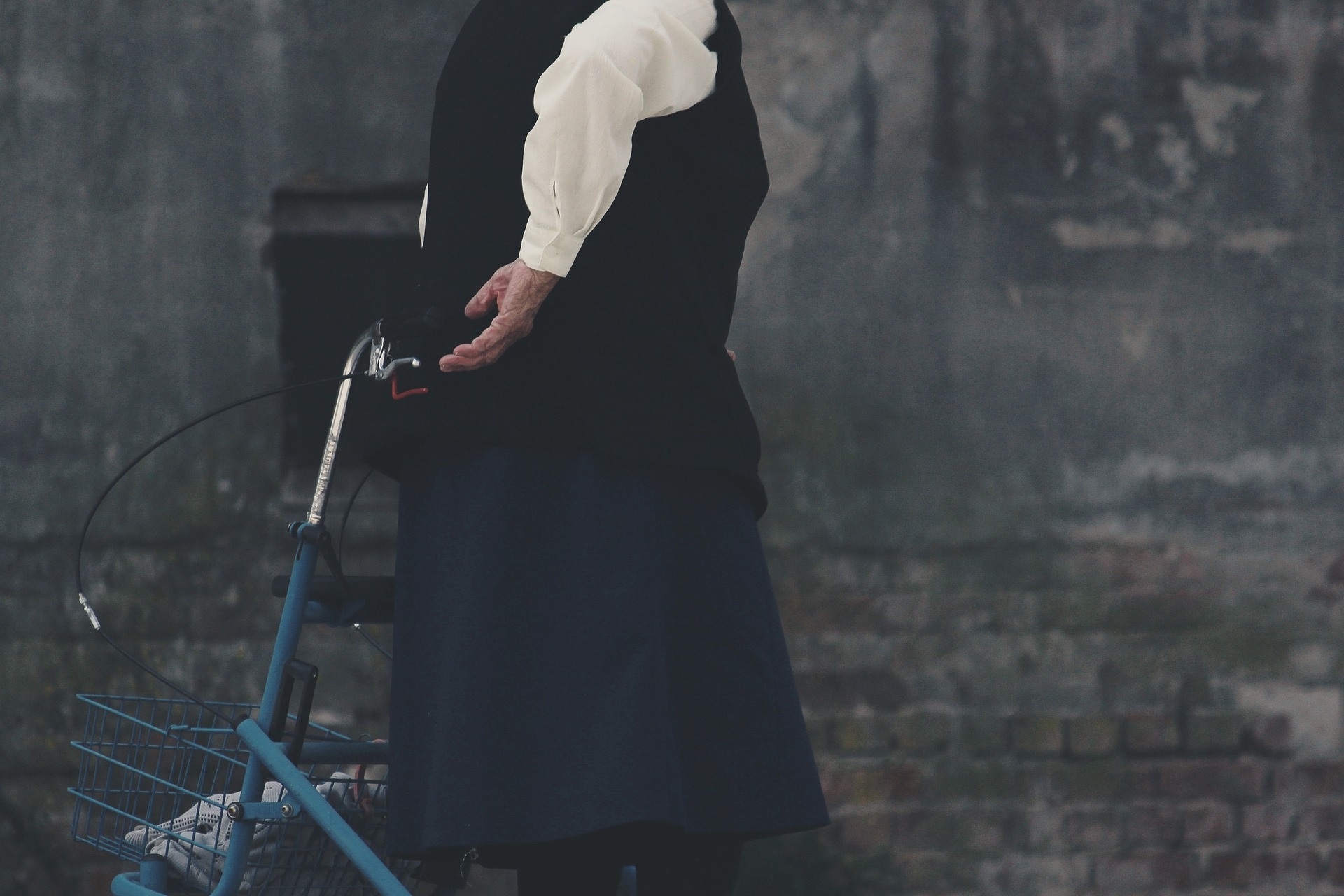
What are the deadlines?
class I medical devices must comply with the requirements of the MDR by the following deadlines:
- Medical devices that were in class I under MDD (93/42/EEC) and are also in class I under MDR (EU 2017/745) must comply with MDR from 26.05.2021.
- Medical devices that were in class I under MDD (93/42/EEC) and are classified in a higher class under MDR (EU 2017/745) have longer transition periods. This is to take into account the greatly increased effort due to the involvement of a notified body. Placing on the market is permitted until 26.05.2024.
- Medical devices that have fallen into classes 1r, 1m, 1s, IIa, IIb, III under the MDD (93/42/EEC) have different deadlines. However, we do not deal with these in this article.
Note: If a deadline other than 26.05.2021 applies in your case, your quality management system must still have met the minimum legal requirements since 26.05.2021!
What does it mean to be a manufacturer?
Example of a Medical device class I
There are different ways in which the role of a manufacturer of medical devices can look exactly. Nevertheless, they all have one thing in common: the company that acts as a manufacturer of a medical device in the legal sense has all the rights and obligations of a manufacturer. To this end, Article 10 of the MDR (EU 2017/745) on the general obligations of manufacturers must be observed in particular. However, there are also aspects of product liability that are relevant.
Scenario 1 - I manufacture medical devices myself: The production of medical devices takes place in my own company. Accordingly, I myself have full responsibility for what happens in production.
Scenario 2 - I put myself none medical devices: The production of medical devices is carried out by a subcontractor. Within the scope of its contractual obligation, the subcontractor is therefore responsible for the performance it provides. It is important to note, however, that you as the manufacturer still have the final responsibility in the legal sense for what happens in production. It is you who places the medical devices on the market and you have the responsibility that these products are MDR-compliant. So you only outsource the production, but never the responsibility!
Scenario 3 - Mixed form of scenario 1 and 2: Some manufacturers have a broader portfolio and produce internally and with subcontractors. Of course, you are also fully responsible for all products placed on the market by you.
Outsourcing of production and procurement of raw materials
It often happens that manufacturers have outsourced the production and at the same time the procurement of the necessary raw materials to a subcontractor. Unfortunately, it often happens that the responsibility for product quality and conformity is assumed to lie with the subcontractor. However, this is not permissible.
You can of course outsource the process of producing and procuring raw materials. However, as already described in scenarios 1 to 3, the responsibility remains with you. In any case, you must sufficiently monitor the internal and outsourced processes to ensure compliance with regulatory requirements.
In the case of outsourced production, this means that you must check and approve the manufacturing processes. Production may only take place according to the agreed processes. And you must check compliance with this, for example, through audits and batch releases. In any case, you should conclude a QAA (quality assurance agreement). In other words, a contract with the subcontractor in which the respective rights and obligations of both sides are comprehensibly regulated. Such a contract also protects you in case of mistakes by the subcontractor. So it really is in your interest to conclude QAAs. A recall quickly leads to costs in the 6-digit range.
If a subcontractor takes over the procurement of raw materials for production, you must also agree on the necessary incoming goods inspections and other in-process controls. As I said, you outsource the procurement, not the responsibility.
Observe the following rule of thumb:
You must monitor and control outsourced processes at least to the same extent as internal processes. You outsource processes, not the responsibility of the medical device manufacturer!
How to fulfil the MDR?
Basically, Article 10 of the MDR entitled "General obligations of manufacturers" gives a good overview of what needs to be done. We present the whole thing in an easier to digest way in the following text. Basically, however, you should note that all of the following points must be fulfilled. It is not sufficient for a legal condition if only some of the points are fulfilled.
Quality management system
Technical documentation
- Every product needs a clinical evaluation.
More information is available here. - Every product needs a risk management file.
More information is available here. - Every product that comes into contact with a patient must be assessed for biocompatibility.
More information is available here. Preparation of an EU declaration of conformity
Logging into DMIDS
Maintenance of the technical documentation
As a manufacturer who exclusively class I medical devices in their portfolio need a quality management system that meets the minimum legal requirements. It is very important to note that such a QM system does not have to be certified according to ISO 9001 or ISO 13485 - but it can be!
Especially for small manufacturers and start-ups who are just venturing into medical technology with a class I product, this advice is very important. The implementation and maintenance of a certified QM system is much more time-consuming than simply covering the minimum legal requirements.
But even if you want to or can take the less time-consuming route - bear in mind that the operation of a QM system takes place parallel to everyday work. This means that you should plan a certain amount of time and effort for it. QM is not something you can document at the end of the year and then be on the safe side.
A functioning QM system is the basis for ensuring that your business model is permanently legal and viable!
A QM system that complies with minimum legal requirements is a system that enables you to play a role in medical technology and the European Union. You have written processes that provide comprehensible guidelines on how to deal with complaints, for example. Because every complaint must be checked by you as a manufacturer to see whether it is a so-called "serious incident". You would then have to report this to your local supervisory authority.
If you do not know what a "serious incident" is: this is also described in processes in a comprehensible way. By means of the QM system, you will be enabled to behave correctly as a manufacturer of medical devices. You are in a position to react to events in a legally compliant manner and can thus make the legally required contribution to the safety of persons and especially patients.
So, in principle, you can think of the QM system as enabling a company to behave like a manufacturer of medical devices.
The technical documentation is created per product. This is basically a product file that must contain evidence that the product meets the legal requirements.
Note: The summary of technical documentation is not described for simplicity.
The legal requirements for products are mainly described in the so-called "general safety and performance requirements" in Annex I of the MDR. It must therefore be checked for each product which of these requirements are applicable. Compliance with all applicable requirements must be demonstrated. This means that documents are necessary. Things like "it has always been like this" or "the product has been on the market for 20 years" are not admissible evidence in the sense of EU 2017/745.
Since we are asked again and again:
Other important components of the technical documentation are detailed information about the production. The manufacturing process must be truly traceable and it must be possible to see where the manufacturing takes place. This also includes all details about the quality controls or in-process controls and a batch release.
For each raw material / component / packaging, the respective supplier must be evident. You therefore need a fully traceable, documented chain from the raw material to the actual medical device. All materials and all bodies involved as well as work steps must be traceable.
In the EU declaration of conformity, you as the manufacturer confirm that the product complies with the requirements of the MDR. This is basically the approval as a medical device of class I. You do not need a certification body or authority for this. However, it must be said that the issuance is not legal if the product does not meet the requirements. The regulatory authorities regularly inspect manufacturers who are newly registered in DMIDS or EUDAMED (more on this later). It is therefore advisable to issue the declaration of conformity only if the technical documentation for the product is available and you have a QM system in place.
The EU Declaration of Conformity must contain the items listed in Annex IV of the MDR. The following image shows the extract of the MDR from Annex IV.
The SRN is the Single Registration Number you receive when you register in EUDAMED. As of today (22.12.2022), the use of EUDAMED is still voluntary because the database is not fully functional. So you may be able to issue the EU DoC (EU Declaration of Conformity) without an SRN for quite a while.
The basic UDI-DI is a unique number that can be used to assign the product to you as the manufacturer. This is not to be confused with the UDI-DI (e.g. GTIN) and the UDI-DI (e.g. batch number + expiry date).
DMIDS is the system currently used in Germany to register as a manufacturer of medical devices with the local authorities. The medical devices that you distribute as a manufacturer are also registered there. The use of DMIDS is currently required by law in Germany. Each member state has own databases.
There is another database or system at European level called EUDAMED. However, EUDAMED is currently not yet fully functional and therefore it is not yet required by law to register devices in EUDAMED. Registration in EUDAMED is therefore currently voluntary for devices.
Your QM system should describe in detail how the technical documentation (TD) can be permanently maintained. Because the TD is not just created once initially and then applies for all eternity.
It is necessary by law to carry out a so-called post-market surveillance. More about this here. This involves the manufacturer checking whether its own product behaves as it should in the market. In other words, it is checked whether the product causes any problems in the market with regard to safety or performance. The resulting findings are stored in the technical documentation.
Risk management must also be constantly updated. For example, you receive a complaint in which a risk or product problem becomes known that has not yet been considered in the risk analysis. Then you have to catch up and update the risk management file.
Also, any changes to the product design, the labels, the instructions for use - everything has to be updated in the technical documentation so that it is always up to date.
Competent authorities & Inspections - Help! What now?
Has your local competent authority registered for an inspection and you are concerned that your technical documentation / QM system is not sufficient?
Has your local competent authority already formulated deviations and set a deadline for you to remedy them?
Please contact us quickly so that a timely response is possible. Together we will find a solution!
Classification dispute: My product is class I - the local authority sees it differently.
In this case, a decision by the BfArM may be necessary. The BfArM writes the following on its website:
"For a demarcation or classification decision by the BfArM, an informal application for classification and/or demarcation must be submitted to the BfArM in accordance with § 6 para. 2 MPDG. In principle, a German notified body, the manufacturer or the competent Land authority are entitled to submit an application."
Experience has shown that there are inconsistencies regarding the classification of class I medical devices in particular when software is involved.
There is a widespread opinion that software as class I is virtually not possible under MDR. However, this is not true. Rule 11 of the MDR clearly describes when software can fall into class I. The rule also clearly describes what a software must not do if one wants to classify a software as class I.
Admittedly, the possibilities of such software in class I are limited. But they do exist. And that is a good thing. Unfortunately, some local authorities see things differently - but in these cases it is advisable to ensure legal certainty by means of a BfArM application.